Jednou z velkých výhod 3D tisku je možnost vyrábět tvarově velmi složité díly, se kterými si tradiční výrobní metody neporadí. Díky tomu lze v kombinaci s výpočetní optimalizací topologie dosahovat velkých úspor hmotnosti při zachování nebo dokonce zlepšení pevnostních vlastností výrobků.
Máte-li vhodné softwarové a hardwarové vybavení, dokážete dnes jako konstruktér a výpočtář zázraky. Jaká magie se skrývá za zaklínadlem „topologická optimalizace“, si ukážeme na příkladu hliníkového držáku převodovky pro elektrickou motokáru.
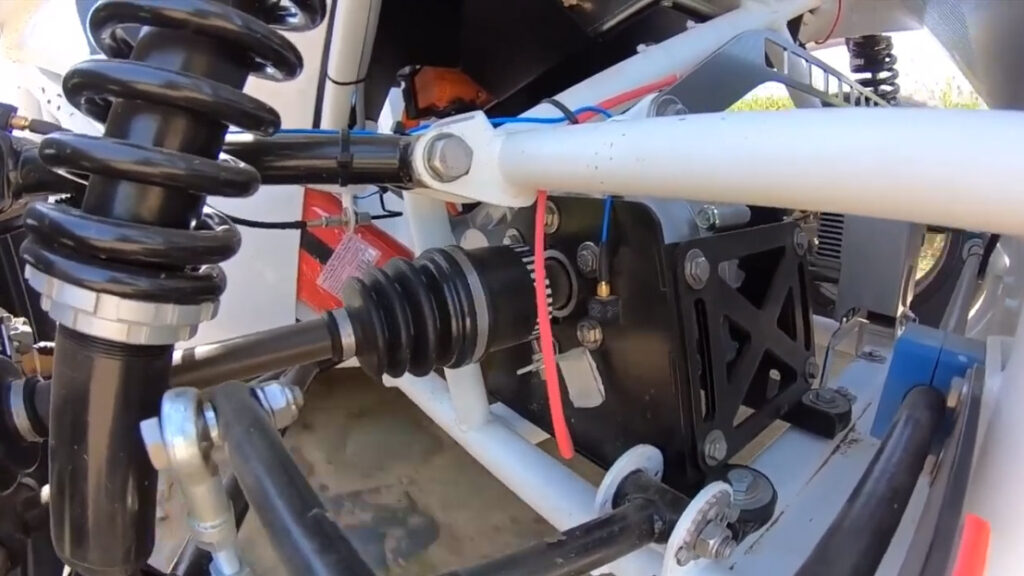
Na začátku je sestava 14 komponent vyráběná tradičně, o celkové hmotnosti 4 kilogramy, na konci téměř dvakrát lehčí držák z jednoho kusu při zachování požadavků na pevnost. Díky použití špičkového softwaru NX od firmy Siemens přitom konstruktér ve spolupráci s výpočtářem a technologem celý úkol zvládli za několik minut.
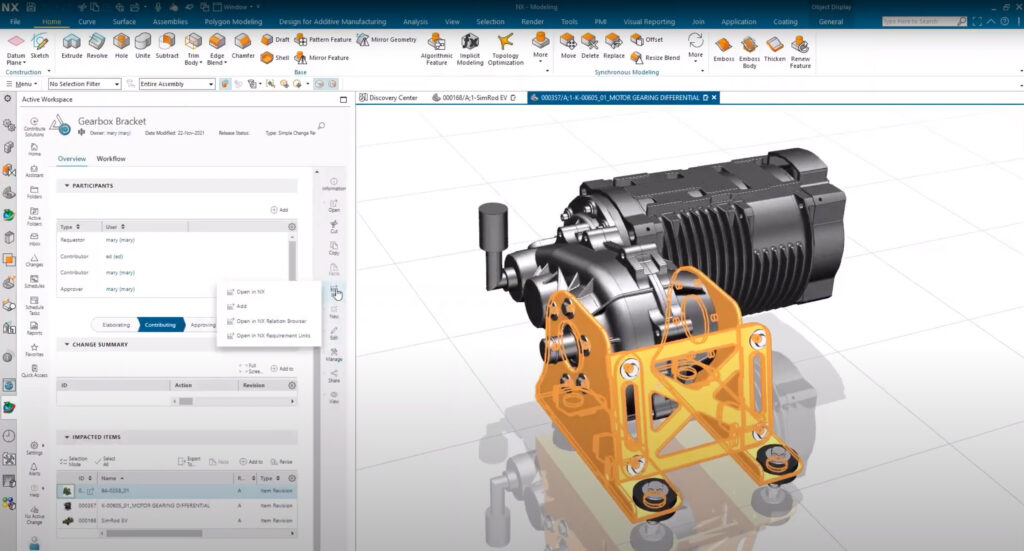
Jejich práce spočívala v šesti navazujících krocích:
- Přípravy původního konstrukčního návrhu pro výpočet topologické studie.
- Automatické provedení topologické optimalizace.
- Ověření optimalizovaného tvaru počítačovou pevnostní simulací.
- Příprava dat pro finální úpravy CNC obráběním.
- Kompletní validace výrobního procesu v CNC stroji.
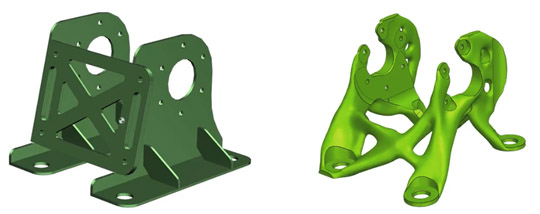
Aby mohl provést topologickou studii, musí konstruktér vymezit prostor, ve kterém může algoritmus generovat novou geometrii a definovat okrajové podmínky, jako jsou veškerá upnutí, prostupy atd.
Na vytvořený zjednodušený model s okrajovými podmínkami aplikuje v příslušných místech známá zatížení.
Generování nejvhodnějšího tvaru prvku, který má nabídnout minimální hmotnost při požadovaných pevnostních vlastnostech, probíhá automaticky a trvá jen několik minut. Výsledek topologické studie obvykle připomíná spíše biologickou než technickou strukturu – ostatně sama evoluce provádí topologické optimalizace s každou novou generací organismů a tyto počítačové hrátky jsou takovým principem doslova inspirovány.
3D model získaný topologickou optimalizací převezme výpočtář, aby jej v CAE prostředí NX podrobil pevnostní simulaci a ověřil, že takto navržený díl obstojí v reálných podmínkách. Pro účely simulace nejprve objekt převede na síťový model (mesh) s potřebným rozlišením, definuje okrajové podmínky v místech upnutí a stanoví střed gravitace tělesa (to proto, že jednou ze složek zatížení je také gravitační zrychlení – na držák budou při akceleraci vozidla působit až 3G).
Pro řešič NASTRAN v systému NX je na dostatečně výkonném hardwaru taková úloha otázkou několika minut. Barevná mapa pomáhá identifikovat místa s rozdílným napětím, které je díky dobrému výchozímu návrhu v tomto případě celkově nízké a díl vyhovuje stanoveným požadavkům.
Předtím, než pošle ověřený díl do výroby, doplní jej konstruktér o nezbytné informace pro výrobu (tzv. PMI), jako jsou rozměrové kóty, požadované tolerance atd.
Prvek má být vyroben z hliníku tavením kovového prášku na 3D tiskárně Renishaw RenAM 500. Technologovi, který bude zakázku zpracovávat, nesmí uniknout, že v některých místech bude vytištěný díl potřebovat dodatečné obrobení na CNC frézce. Proto je potřeba v příslušných místech topologicky optimalizovaného CAD modelu přidat materiál, aby takzvaně bylo kde brát. Jelikož se navzdory komplikovaným tvarům v NX stále jedná o parametrický model, je úprava ploch i děr a aplikování přídavků materiálu mnohem snazší než kdyby bylo potřeba zasahovat do geometrie ve formě síťového modelu.
3D tisk kovových dílů s využitím laseru je složitý proces, při kterém je potřeba předcházet nežádoucím teplotním deformacím výrobku. Hodně při tom pomůže výběr té nejvhodnější možné prostorové orientace dílu v tiskové komoře, což u tvarově složitých dílů člověk nedokáže žádným způsobem odhadnout na základě intuice. I zde proto přichází na řadu počítačová simulace, a to celá řada mnoha desítek iterací, při kterých algoritmus posuzuje nejrůznější možné polohy dílu a hledá tu, při které dojde vlivem přenosu tepla k nejmenšímu možnému kroucení prvků.
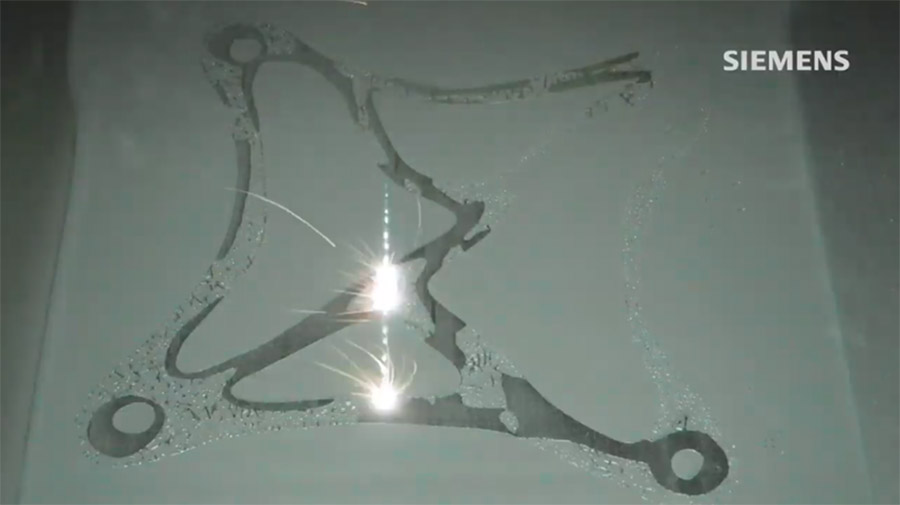
Jelikož se jedná o výpočetně velmi náročnou úlohu, svěřili výpočtáři její provedení na cloudový server (v tomto případě přes integrovanou aplikaci NX Build Optimizer). Vedle nejvhodnější orientace dílu při tisku software zoptimalizuje také návrh ideálních podpěr, které přenášejí gravitační a tepelné zatížení.
Z takto připravených dat již lze připravit tiskovou úlohu, jejíž finální nastavení je kontrolováno na samotné 3D tiskárně.
Vytištěný díl je potřeba zbavit podpůrných struktur a doladit CNC frézováním, aby byla v potřebných místech dosažena požadovaná přesnost a kvalita povrchu.
Pokud využijete robustní platformu jako je zde popisovaný systém NX, můžete hladce pokračovat s původními 3D daty také při přípravě obrábění a validaci výrobního procesu. K dispozici vám bude mj. kompletní digitální dvojče vybraného obráběcího stroje, ve kterém si pohlídáte veškeré případné kolize a připravíte bezproblémový NC kód.
Výsledkem celého snažení je topologicky optimalizovaný hliníkový díl o hmotnosti 2,5 kg, namísto předešlé sestavy ze 14 dílů, vážící 4 kilogramy.
K provádění topologické optimalizace konstrukce je dnes k dispozici hned několik softwarových řešení. K ilustraci jejích principů a všeho, co taková studie obnáší, jsme v tomto případě využili platformu NX, která díky systematické integraci všech potřebných nástrojů a aplikací do jednoho ekosystému umožní přímočarou návaznost v jednotlivých krocích – od designové skici přes veškeré simulace po přípravu dat k výrobě a jejich validaci.
Obrázky a fotografie použité v tomto článku pochází z následujícího videa společnosti Siemens: